The Impact of 360 Rotating Telehandlers on the Housing Market
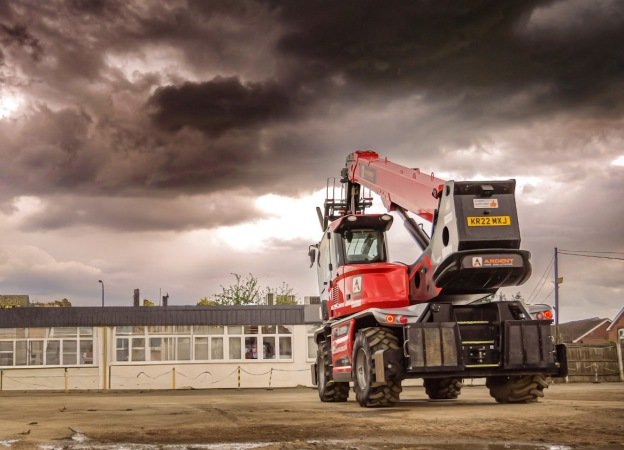
In recent years, the housing market has witnessed a transformation, not just in design and materials but also in the technology used to construct homes. One key piece of equipment driving this change is the 360 rotating telehandler. These versatile machines, often referred to as "rotos," are revolutionising construction practices, improving efficiency, safety, and reducing costs, which in turn is influencing how homes are built and sold. Here's how:
1. Enhanced Efficiency and Versatility
360 rotating telehandlers have set a new benchmark in construction flexibility. Unlike traditional forklifts or cranes, telehandlers with 360-degree rotation can easily navigate confined spaces typical of urban housing projects or high-density developments. This maneuverability allows operators to reach areas that would otherwise require multiple machines or repositioning, saving time and labor costs. Builders can access tight spots, move materials across various heights, and rotate without moving the base, streamlining the construction process.
For the housing market, this increased efficiency means that projects can be completed faster. Faster construction times reduce costs, making housing developments more affordable, which is crucial in markets where housing demand often outpaces supply.
2. Safer Worksites, Fewer Accidents
Safety is a top priority in any construction project, and telehandlers with 360-degree rotation bring significant safety advantages. The ability to handle heavy loads from a stationary position with full rotation reduces the need for excessive machine movement, minimising the risk of accidents on congested worksites. With fewer machines required for various tasks, worker safety improves as there are fewer collisions, and the overall risk of falling materials or missteps decreases.
For the housing market, this translates into fewer delays caused by on-site accidents or safety violations. Insurance costs may also be lower, as safer worksites often lead to fewer claims, benefiting both developers and homeowners.
3. Cost Savings Leading to Affordable Housing
By combining the functions of multiple machines, 360 rotating telehandlers reduce the need for additional equipment on-site. With one machine capable of handling multiple tasks – such as lifting, loading, and rotating – project managers save on equipment rental and maintenance costs. This cost efficiency trickles down the supply chain, impacting the overall budget for a housing development.
4. Supporting Green Building Initiatives
With the increasing emphasis on sustainability, 360 rotating telehandlers can support green building initiatives by reducing the carbon footprint associated with construction. These machines are often more energy-efficient than traditional equipment, consuming less fuel due to their multifunctionality and reduced movement on-site. Additionally, Ardent Hire have offsett all carbon produced from it's entire roto telehandler fleet, meening all roto operator hires are carbon netural.
This aligns with the housing market's push toward more sustainable, energy-efficient homes. Buyers are increasingly prioritising eco-friendly properties, and reducing the environmental footprint of the construction process can be a key selling point.
Conclusion: A Game Changer for Housing Development
The 360 rotating telehandler is not just a construction tool—it’s an enabler of faster, safer, and more cost-effective housing developments. As the demand for affordable, sustainable housing continues to rise, the use of innovative equipment like telehandlers will likely become a standard practice. By improving efficiency, reducing costs, and supporting safety and sustainability goals, these machines are helping to shape the future of the housing market, one construction site at a time.
As the industry evolves, we can expect more builders to adopt this technology, ultimately leading to faster, greener, and more affordable housing options for our local communities.